#FantasticFibres: Going Bananas
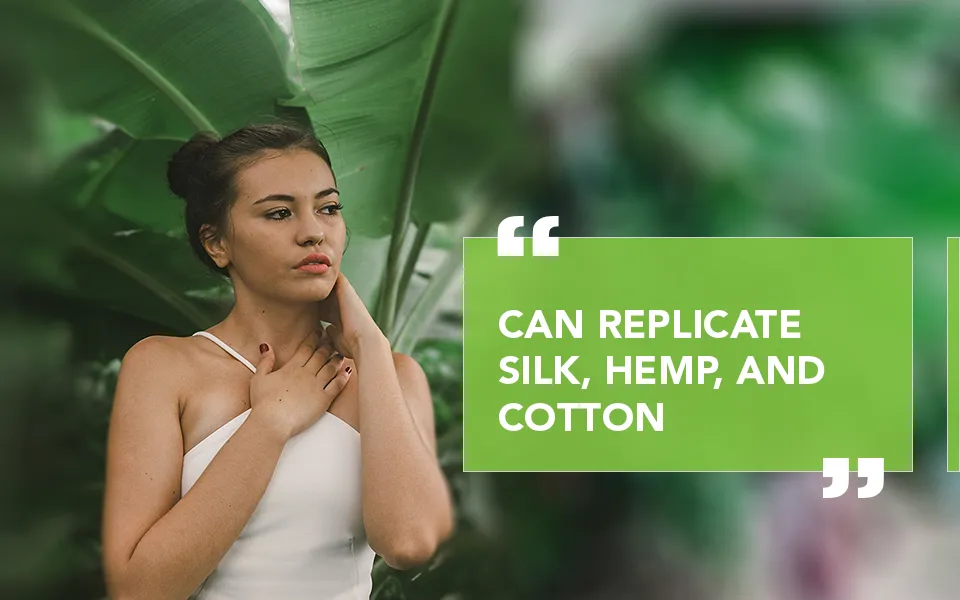
Fun fact: there are around one thousand different varieties of banana, but most people are only familiar with two. This fruit family is one of the most popular foods worldwide, but almost entirely restricted to its Cavendish and plantain forms. The other 998 stay largely locally grown and used, but in some pretty nifty ways – including to make cloth. Using different parts of different banana varieties, multiple types of banana fibre eco-fabric can be made. This lightweight fibre is a heavyweight in the world of sustainable fashion with its ability to replicate silk with the softer inner leaf fibre, or more durable fabrics like hemp with stem and outer leaf fibre. And a little goes a long way – it requires much less plant material to create a yard of cloth than almost any other fibre.
The Origin Story
Much like pineapple, using banana fibre as the basis for clothing and household goods is not new. It has actually been around since the 13th century in Southeast Asia and Japan. Nowadays, however, it’s mostly manufactured for local use, or to appeal to the sustainable fashion market. Currently, India is the largest producer of banana fibre by virtue of being the largest producer of bananas worldwide. One standout fact is that only 37 kilograms of banana leaf sheaths are needed to make one kilogram of fabric. That might seem like a lot, but it is tiny compared to the viable amount harvested from cotton or pineapple, for example.
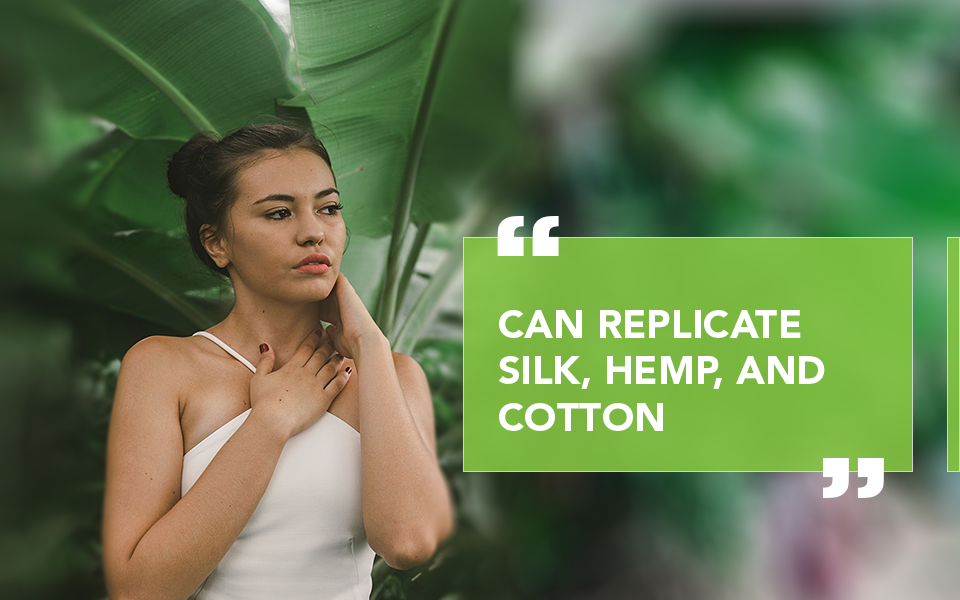
There are 3 main products of this fibre – “banana silk”, banana cotton blends, and musa fibre, formerly known as “Manila hemp.” The oldest and most common is musa fibre, made using the fibres in the stem and outer leaves of the abaca-banana plant. Historically called “Manila hemp” because the Philippines was the biggest producer, the fabric made from the stems and toughest part of banana leaves is primed to be a competitor to hemp and conventional cotton. Its claim to fame is being one of the most durable plant fibres on the planet, and naturally has been used for centuries to make rope, woven textiles, and floor mats. Today, producers of it have branched out to make everything from teabags to outerwear and accessories with it as well. Outer leaf/stem banana fibre can pose a challenge for producers because of its toughness, but also has high potential rewards with its next-level durability and strength!
There’s Always Money in the Bananas
Musa fibre might have previously been the most popular child of the banana fibre family, but the younger inner leaf fibre is quickly catching up. The fabric made from inside of the banana leaf is packed with benefits. It’s biodegradable, moisture-wicking, piling and wrinkle resistant, and obviously vegan. The final product’s texture mimics silk, with all of its lightweight and breathable goodness for warm weather and hot climates – without the animal welfare issues. The inner stem and leaf strands are also easily blended with cotton for a lightweight, more sustainable multi-purpose fabric. Rumour has it that banana fibre has many of the traits and benefits of bamboo, but with a lower-impact manufacturing process and higher tensile strength, spinnability, and texture quality.
So far, there are few producers of banana fibre out there, but what is available is almost certainly eco-conscious. Offset Warehouse is one option that partners with local artisans to harvest banana fibres and create the fibre using traditional carbon-neutral techniques. Some firms use the inedible abaca plant’s giant leaf sheaths for their banana fibre, others, like Green Banana Paper, choose to use the offshoots from breakfast alpha fruit Cavendish banana plant. This choice means resource (water, land, etc.) and pesticide use per banana plant is more worthwhile than if they just went into creating one product, a common theme in our #FantasticFibres selections. Banana trees only bear fruit once in their life and are then torn down to plant replacements, so using the stems for textiles lowers agricultural waste. It also embodies the zero-waste adage of old – use every part of the plant or suffer the ecological consequences. Plus, the profits of selling banana leaf sheaths goes back to the farmers, so they get extra income for minimal extra labour.
Will You Go Banana?
Resulting from the niche and handmade nature of current banana fibre offerings, the fabric is currently pricey and labour-intensive. The process of turning leaf/stem fibre into cloth is mostly electricity-free using traditional handloom methods, resulting in a carbon neutral product, but also a more expensive one. Banana “silk” is also less durable than its hemp-like sibling, and requires a light touch much like true silk. Banana fibre born from trees grown for agriculture are also often coated in harmful pesticides for both farm workers and the surrounding waters, though abaca varieties typically avoid this issue. The flip side of this argument is that fewer pesticides are being used than if two separate plants were grown to create both the fruit and the fabric. Also, organic and Fair Trade bananas and consequently banana fibre exist too.
This makes banana fibre an incredibly versatile option worthy of more credit than it has received so far! Banana fibre can be used to replicate silk, hemp, and even cotton, or easily be blended with other natural fibres to offer its benefits at a lower cost. “Going bananas” is normally used as a negative descriptor, but in this case, we think that sounds pretty good.